Stringing innovation
Senior picks up unique skills to build his own guitar from scratch
photo courtesy of Thomas Detlefsen
Clamping all the wood pieces together, senior Thomas Detlefsen wanted to get an idea for how his guitar would look semi-completed, without using glue. He just finished sanding the body of the guitar and had few more things to add to it. “Here I finished sanding on my body and decided to dry clamp all my wood pieces together without any glue along with a few pieces of hardware to get a rough idea of what the guitar would look like when it’s finally complete,” Detlefsen said. “After the whole process, it was satisfying to finally see it come together and start to look like a finished project, especially one that so closely resembles the original guitar it’s based on.”
March 11, 2021
Creating an organized plan, acquiring assorted materials and spending numerous hours perfecting the craft are just a few things that any artisan might do on any given DIY project. Currently in Advanced Carpentry class, senior Thomas Detlefsen, has been building his own custom guitar since September.
Having a magnificent deal of passion for music, Detlefsen has constantly immersed himself with the various arts of music. Detlefsen taught himself how to play the guitar at an early age in middle school and still continues to play today. Since then, he has played numerous covers on popular songs, ranging from the artist Tom Petty to the Creedence Clearwater Revival musical group with numerous acquaintances. Music to Detlefsen is more than just a hobby, as it is one of his joys that he dedicates a lot of devotion to.
“I’m currently almost done building my guitar, and I hope to complete the construction by the end of the semester,” Detlefsen said. “It has been a day-to-day process, and I have to spend a lot of time understanding and applying new techniques that I didn’t have prior knowledge of. YouTube videos have helped me gain new expertise and it has guided me through some of the unfamiliar processes.”
Getting his influential inspiration from the Beatles lead guitarist, George Harrison, Detlefsen is currently replicating a guitar model named the Rickenbacker with the Mapleglo finish. This is highly similar to the 360/12c63 Guitar with the Fireglo finish that George Harrison used during his vast music career. Detlefsen’s guitar will have 12 strings, as opposed to many guitars today having only six strings. Materials and hardware are often outsourced either by the school or have to be ordered from official various suppliers.
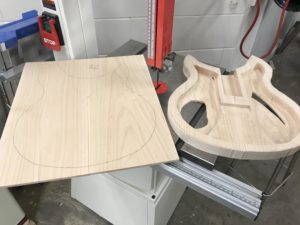
“There are different parts and components of the guitar that need to be designed separately,” Detlefsen said. “I still need to assemble everything together and glue everything down for the final product. I also started bringing my guitar home to work on last week, since I have free time to work on it. This allows me to speed up the process and get ahead with the development of the guitar, as I want to complete it by the end of the semester.”
In Detlefsen’s Advanced Carpentry class, students have the option to choose what project they want to work on, during the course of the semester. Other students have created various crafts such as tables and desks for their projects over the course of years.
“This year, we had two students who decided to create a guitar for their project, ” skilled and technical science teacher Mitchell Mentzer said. “I helped to get their CNC programs set up correctly so that all the different components would be arranged properly. Any time you have hand-based learning, students can get the ability to create and design anything they desire and really immerse themselves with their project.”
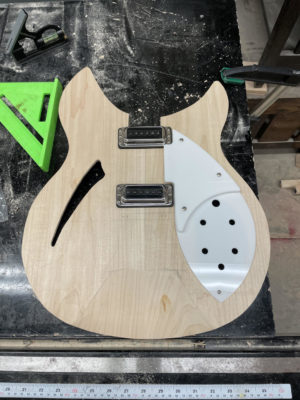
Likewise, other students in the class have also challenged themselves to construct a guitar from scratch, such as senior Nickolas Mathis. Mathis also hopes that his hard work and dedication to this project will pay off once the guitar is complete.
“I enjoy knowing that what I’m creating will turn out precisely to the design I had made for the guitar and it will hopefully play to the way I intend it to,” Mathis said. “Some of the challenges I’ve faced was shaping the neck to the correct width, using the CNC Miller correctly, and sanding everything entirely, which usually takes hours to complete.”
As a result, Detlefsen has also committed a lot of time and effort towards his guitar. Occasionally, hardships and adversity can spontaneously occur with no short notice.
“Aligning the neck of the guitar to the body of the guitar has been a great difficulty,” Detlefsen said. “This process is crucial to get done perfectly, as it will highly impact the ability to play the guitar. The biggest setback occurred today when I accidentally cut myself with the table saw and had to attend urgent medical care.”
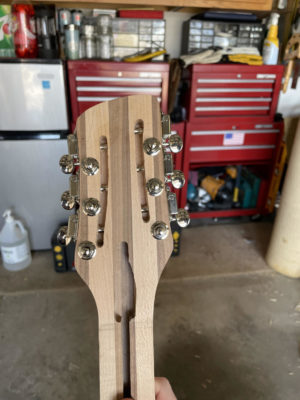
Ultimately, Detlefsen hopes that this overall experience will not only inspire him to do more with music but also help him understand the behind-the-scenes of how instruments can produce unique sounds.
“The amount of precision needed and creating a unique guitar that some may associate to the real deal would be very humbling if people noticed,” Detlefsen said. “The fact that I built a replica from scratch that is very iconic can be very inspiring to others.”
Detlefsen is expected to finish his one-of-a-kind guitar in the coming days and hopes to use his creation in many future musical downtimes that he has.